Steps to Install a New Elevator in Your Building
Installing a new elevator in your building is a significant project that requires careful planning and execution. Whether you’re upgrading an existing system or adding a new one, understanding the steps involved can make the process smoother and more efficient.
A well-installed elevator enhances accessibility and adds value to your property, making it a worthwhile investment. This guide will walk you through these steps to help you achieve a seamless elevator installation for your building.
Planning and Preparation
Assessing building requirements is the first step in installing a new elevator. You need to look at the building’s structure, the number of floors, and the amount of space available for the elevator. Analyzing these factors will help you determine the type and size of the elevator that will best fit your needs. You also need to consider the traffic patterns within the building to ensure the elevator will be able to handle the expected load.
Budgeting and financing options come next. Installing an elevator is a big investment, so having a clear budget is essential. Researching the costs involved, from equipment to labor, will give you a good idea of what to expect. Also, look into various financing options. Some projects might qualify for loans or grants, especially if the elevator improves accessibility.
Securing permits and approvals is a must before any installation can begin. Different areas have different regulations, so it’s important to check with local authorities. You might need permits for construction, electrical work, and more. Obtaining the necessary approvals not only helps you avoid legal issues but also ensures that your elevator will meet safety standards.
Choosing the Right Elevator System
Choosing the right elevator system involves considering various factors. One of the first things to decide is the type of elevator that will best suit your building. There are several types to choose from, including hydraulic elevators, traction elevators, and machine-room-less (MRL) elevators. Hydraulic elevators are often used for lower buildings, while traction elevators are better for taller structures. MRL elevators offer a space-saving option.
Another key point is considering capacity and speed. Understanding how many people need to use the elevator and how quickly they need to move between floors will help you select the right system. Elevators come in various sizes and capacities, so make sure to choose one that fits the expected usage. The speed of the elevator is also important, especially in taller buildings where faster speeds can save significant time.
Evaluating energy efficiency and sustainability is becoming increasingly important. Energy-efficient elevators can significantly reduce operating costs over time. Look for systems that use less power and have features like regenerative drives, which can feed energy back into the building’s electrical system. Sustainable materials and eco-friendly designs are also worth considering to minimize your elevator’s environmental impact.
Installation Process
Preparing the site is the first step in the installation process. This involves making any necessary structural adjustments to accommodate the new elevator. You might need to reinforce the walls, floors, or ceilings where the elevator will be installed. Clear the area of obstructions and ensure that the site is safe for the installation team to work.
Next comes installing the elevator components. This includes setting up the shaft, the cab, the motor, and the control systems. The installation crew will assemble the elevator parts according to the manufacturer’s specifications. This step is critical to ensure the elevator operates smoothly and safely. Each component needs to be installed with precision to avoid any issues later on.
Conducting safety checks and initial tests is the final step in the installation process. The elevator must undergo a series of rigorous safety inspections to ensure everything is working correctly. These checks cover the mechanical and electrical systems, ensuring that all safety features are operating as they should. Initial tests will also be performed to make sure the elevator runs smoothly and efficiently before it is opened to the public.
Post-Installation Tasks
After the elevator is installed, final inspections and certifications are necessary. These inspections confirm that the elevator meets all local and national safety standards. Inspectors will check all the systems again and issue the required certifications. This step is crucial to ensure the elevator is safe for use and complies with all regulations.
Training for building staff and users is the next essential task. The elevator installation team will provide training to the building's maintenance staff on how to operate and manage the elevator safely. They will also educate them on basic troubleshooting and emergency procedures. Informing regular users about proper elevator use can prevent misuse and ensure smooth operation.
Scheduling regular maintenance steps is the last but equally important task. Elevators require ongoing maintenance to keep them running efficiently and safely. Regular maintenance checks can help identify and fix minor issues before they become major problems. Creating a maintenance schedule and sticking to it can extend the life of the elevator and maintain its performance.
Conclusion
Installing a new elevator involves several detailed steps, from planning and preparation to post-installation tasks. Each phase is crucial and requires careful attention to ensure a smooth and successful installation. Following these steps will not only ensure the safety and efficiency of your elevator but will also enhance the overall value and accessibility of your building.
If you’re considering installing a new elevator in your building, take action now. Don’t delay in improving the safety and accessibility of your property. Elevator Solutions Inc. is here to help guide you through every step of the process. Contact us today to start planning your new
elevator installation.
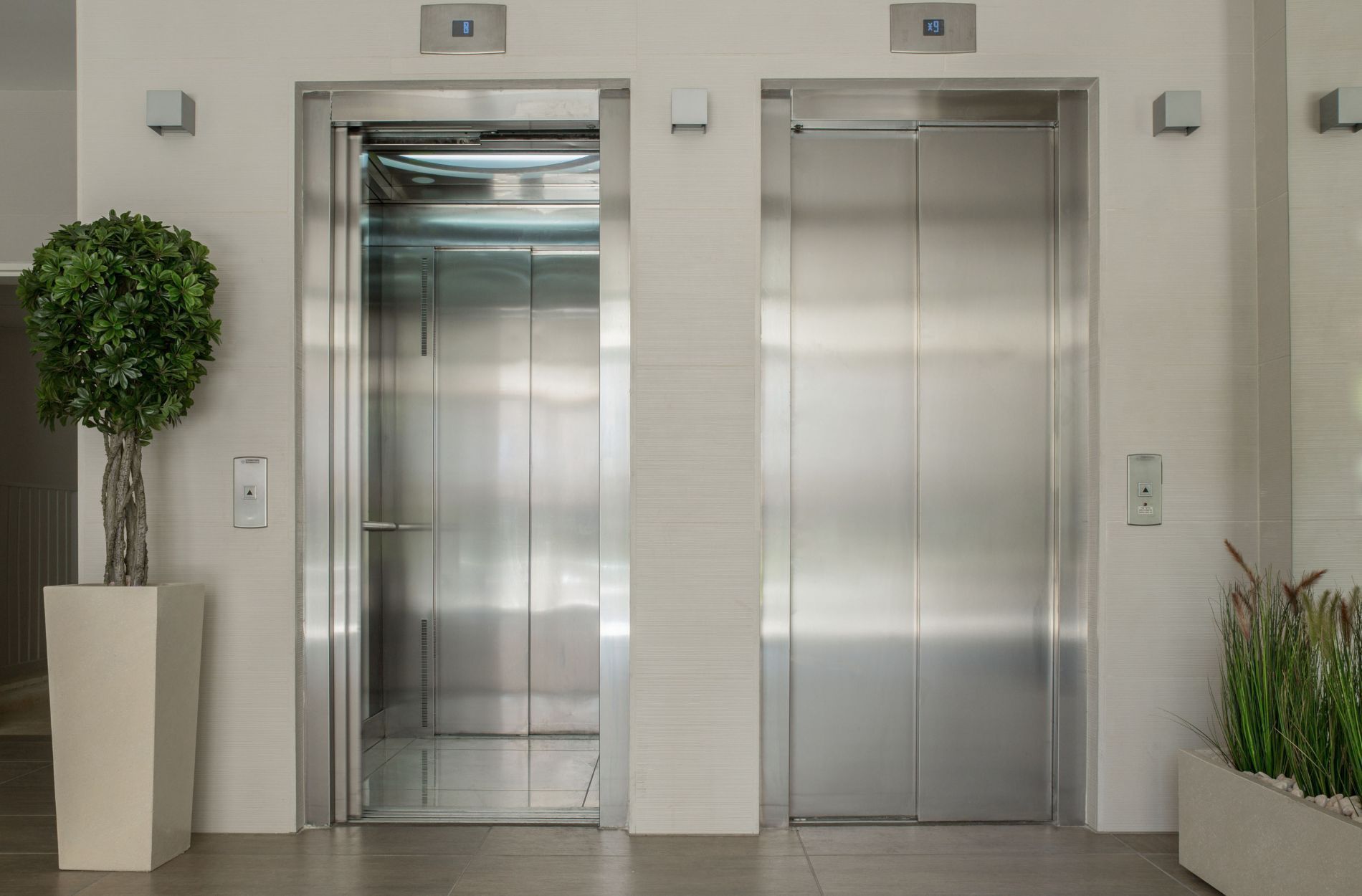